Hi there,
Been a while again but good news, I was busy with building rather than blogging 😀.
And yes I passed my welding exam and yes I learned a lot again while building.
As this design is well constructed and I guess drawn in a CAD program all the parts should fit like a glove. In a wooden version a gap of an extra milimeter or 2-4 is not a problem as you dab an extra dot of epoxy with filler to solve it. For welding it is important to have no gaps at all as that is the easyest way of welding.
So I learned 2 important skills: Bending and filling.
When to parts aren't fitting that means that the curve of the panels isn't right yet. But with these fish-like shapes it takes a while to find out where to bend (or stretch) in order to close a gap. And sometimes you have to bend a panel about two meters aft (or forward) from the gap. Now with a bit of experience I now am able to make the panels fit quite accurately. And - not a surprize of course - it smooths the curves of the hull as well.
Second skill is fillet-welding. Once I found the right settings for my welding machine for the various positions I was able to close the remaining small gaps with a fillet-weld. This gives me more confidence to get the vessel watertight after all 💦😂.
In the pictures below I'll show you some stages of the deck build up from the past few weeks.
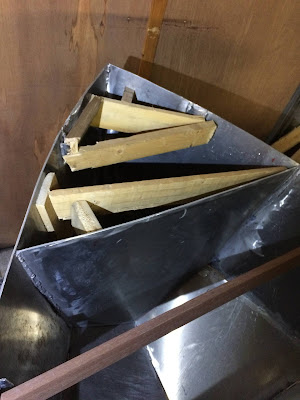
Picture right: I was extremely satisfied that I was able to shape the bow section smoothly. I used the deck template for the right curves and it took some timber to get there. Aluminum doesn't react the same as wood and it didn't follow a smooth curve around the bulkheads. In particularly after I welded the bulkheads the panels waved in stead of following a smooth curve due to heath schrinkage.
In the cockpit and cabin area it was quite easy to make the panels fit. I allready spread the sides to fit the seat panels and just a last milimeter was needed to close all the gaps between the lower and the upper side panels. (picture below)
Rest of the pictures is about building up the backrests and the aft cabin wall:
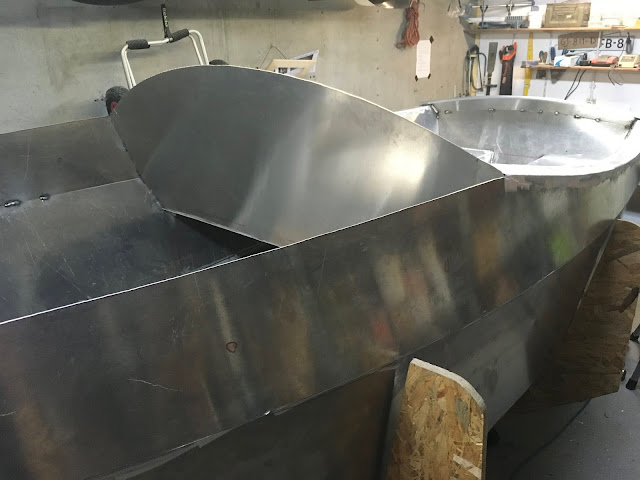
And final result of the transom made with a 22 mm aluminum tube: